1. Sustainable tire compounds
As reported throughout 2023, considerable progress is being made with the development of tire compounds comprising a high percentage – typically ranging from 40-90% – of ‘sustainable’ materials. As well as helping to meet their own net-zero goals, these advances by major tire makers are essential for suppliers and developers of bio-based and/or recyclate-based polymers, fillers, additives and chemicals. A clear example is the recovered carbon black industry, where producers need a major ramp-up in demand to support future investment plans. It’s a similar story for many other supply-chains, such as those tapping residual materials from the wood & paper industries, agricultural waste, end-of-life tires, recycled steel, and PET packaging. While still early days, the pioneering suppliers will be hoping for further developments such as:
- The Pirelli P Zero E – a UHP tire with over 55% of materials sourced from natural and recycled origins that also reduces tire wear by 42% – recently named ‘tire of the year’ at the 2023 Automobile Awards in Paris;
- Continental’s ‘industry first’ volume production of the UltraContact NXT tires incorporating up to 65% renewable, recycled or ISCC Plus certified materials, while delivering “the highest" EU tire-label ratings for rolling resistance, wet braking and exterior noise;
- Michelin’s road-approved car tire containing 45% sustainable materials that incorporate technologies expected to feature in standard tires in 2025. The tire is part of Michelin’s broader sustainability ambition to produce all tires with 100% sustainable - renewable or recycled -materials by 2050, with an interim target of 40% on average by 2030.
2. New tire plant projects in Europe
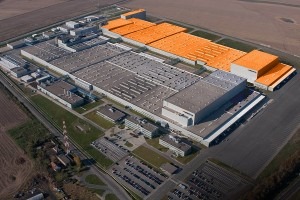
For all the well-documented challenges facing the region’s tire manufacturing sector right now, Europe continues to be the focus of major investment projects by leading industry players. In November, Hankook announced a €540-million investment to add production capacity for truck and bus radial (TBR) tires at its site in Racalmas, Hungary. The project, it said, will increase output capacity by 800,000 units per year by 2027, and create 450 new jobs. Meanwhile, Chinese tire maker Qingdao Sentury Tire Co. is continuing work on a €550-million plan (revealed in January) to establish greenfield tire production project in in Galicia, northwest Spain, with an annual output of 12 million tires for light vehicles. And, in May, Nokian Tyres plc broke ground on construction of its greenfield tire manufacturing plant in the north western Romanian town of Oradea. The €650-million project will have capacity to produce 6 million passenger car tires when fully ramped up. First tires are expected to be rolled out in the second half of 2024 with commercial operation set for early 2025. In another potentially significant development, Linglong recently revealed that it is shifting production of some TBR tires for the US market from Thailand to Serbia, in order to counter potential trade barriers. Also, in July, Pirelli revealed plans to invest €400 million in its plants in Romania and North America to increase its ‘high value’ tire production capacity at the locations by the end of 2025.
3. AI factory of the future
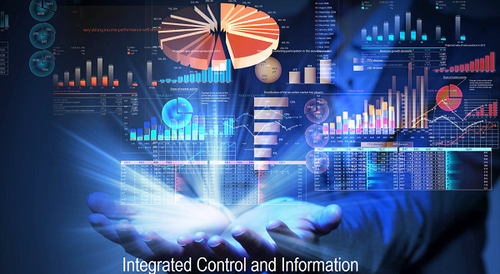
While AI technologies will eventually permeate all areas of tire & rubber-product manufacture, large-scale adoption will initially be the domain of the very largest players. Even among major tire makers, just a select few have the resources to invest in the high-end development work and recruit the IT-savvy people needed to apply AI and machine-learning across their manufacturing processes. As Jordan Reynolds of Kalypso explained in March, the adoption of AI technologies will be part of a wider evolution in which tire and rubber-product factories become “meticulously focused” on gathering data, for every parameter at every stage of production. Moreover, he said, this data will be used to build highly realistic models of how the processes operate under different conditions towards achieving greater levels of real-time control, reducing disruption and downtime, and delivering much higher production yields. Eventually, predicted Reynolds, these new levels of control will enable factories to become more precise in terms of serving the market and so become more specialised and localised.
4. Departure of Richard Kramer
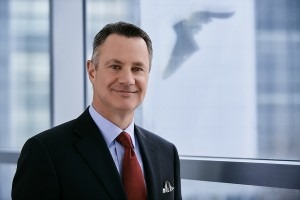
Few, if any, current executives in the global tire manufacturing sector could rival the experience, market-knowledge and industry-wide respect garnered by Goodyear's soon-to-be ex-leader. But with reversals in business results, particularly since the Covid pandemic, came calls from activist investors for a change in leadership and strategic direction. With little sign of recovery on the immediate horizon, these pressures culminated in US group's announcement in November that its long-time chairman, president and CEO Richard Kramer was to be replaced by a yet-to-be-found successor. In its statement, the investor-led board acknowledged that Kramer had delivered the “five highest years of annual segment operating income” in the group’s history, steered it through the global pandemic and led its largest-ever acquisition – Cooper Tire – in 2021. Ironically, it seems that the overlap of the latter two events left Goodyear particularly exposed to the market difficulties that have since arisen. Time will tell if the management rejig and a new strategy involving divestments and capacity closures are the best way forward for Goodyear’s shareholders, employees and other stakeholders.
5. World’s largest synthetic rubber producer
In May, the International Institute of Synthetic Rubber Producers (IISRP) released annual figures showing that Sinopec had emerged as the world’s largest producer of synthetic rubber materials. According to the latest production data, the Chinese petrochemicals major reached an active capacity of 1,878 kilotonnes (kt) – ousting the long-established leader Arlanxeo, which had an active capacity of 1874kt. Meanwhile, another China-based producer PetroChina strengthened its hold on third slot with an active SR production capacity of 1,355kt. This year’s changes at the top of the IISRP table had been anticipated: over recent years, capacity-expansion in China has far outpaced that seen in any other global region. In itself, this trend should not unseat Europe from its traditional position at the centre of the world’s synthetic rubber industry. However, the milestone reached by Sinopec is in chime with a continuing shift in the production of tires and other rubber-based products to China and elsewhere in Asia.
6. High hopes for hydrogen
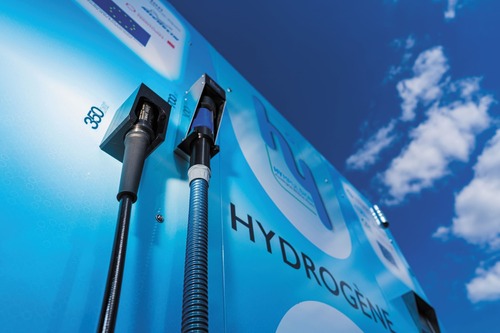
The fast-developing hydrogen fuel sector emerged more clearly as one of the brightest new market prospects for the rubber industry in 2023. To fully realise the potential of molecular hydrogen in new-energy and new-mobility applications, these industries need a broad range of elastomer-based technologies to ensure safe transport and containment of H2. The technical challenges include the enormous stresses placed on sealing systems, while temperature ranges of -40°C to 85°C can occur during refuelling operations, Among the leading rubber processors advancing solutions to tapping the potential of the world’s smallest molecule this year were: Michelin via the Symbio JV, ContiTech, Datwyler, Freudenberg and Trelleborg. Watch out for further development from these and other players in 2024.
7. Tire wear particles and 6PPD
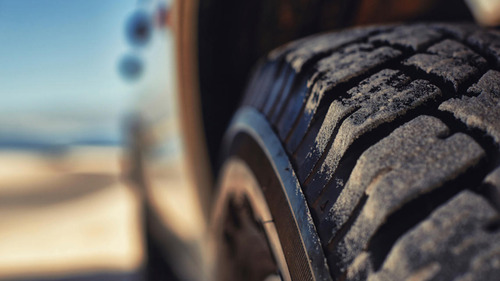
Industry efforts to find alternatives to 6-para-phenylene-diamine (6PPD) antioxidant in tires moved up several gears in 2023. Tire wear particles have been linked to deaths of coho salmon and trout in the US: caused by 6PPD-quinone, formed by the oxidation of the rubber stabiliser. As Nick Molden, founder of UK-based Emissions Analytics, advised, tire wear toxicity “is a challenge to get ahead on, because it is harder [than others] to solve and potentially more problematic. Meanwhile, the US Tire Manufacturers Association has warned against any “premature” prohibition on the use of 6PPD in tires: “It is not a simple process to change the composition of tires; any change could affect the stopping distance of tires, durability, vehicle fuel economy, tire wear and other safety-related components.” But there have been some promising advances in this arena, not least Asahi Kasei’s development of technology to reduce the need for 6PPD by improving the inherent ozone resistance of tire rubber. Using a ‘unique’ hydrogenation catalyst and novel process technology, it has achieved controlled selective hydrogenation of SBR to optimise the balance between ozone resistance and compatibility with other rubbers.
8. EU proposals to ban fluoropolymers
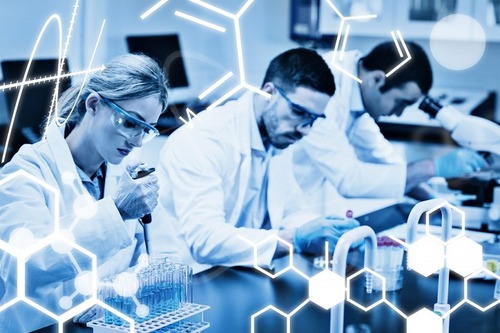
The European Chemical Agency (ECHA) on 22 March announced proposals to ban all per- and poly-fluoroalkyl substances (PFAS), including fluoroelastomers and other fluorinated polymers. The proposals, it stated, were prepared by authorities in Denmark, Germany, The Netherlands, Norway and Sweden. Concern over ‘persistency’ was the main justification for the "total ban", the five authorities also deciding that a substance-by-substance approach would be too slow. The decision not to differentiate between different families among PFAS means that more than 10,000 substances could be eliminated from the market by 2025. Moreover, as the proposed restrictions cover the manufacture, production, import and use of PFAS in an article or as a raw material, the move could have a devasting impact on vast tranches of EU industry, not least the automotive, aerospace, chemicals, ‘green energy and semi-conductor sectors. All eyes now are on how the ECHA committees and five national authorities deal with the massive amount of detailed input provided to the public consultation process regarding this 'wrecking-ball' approach to legislation.
9. Tire capacity restructuring in Europe
November saw a shock series of tire plant closures in Germany: by Goodyear, at Fulda (1,500 jobs, 21,000 LV tires/day) and Furstenwalde (700 jobs, 10k HV tires/day); and Michelin, at Bad-Kreuznach (1290 jobs, 26k LV tires/day); Homburg (1,280 jobs, 4k HV tires/day) and Karlsruhe (593 jobs, 5k HV tires/day). As well as high energy and other production costs, the moves are linked to lower growth prospects and increasing competition from budget tires in the EU region. Plans to add new capacity are, therefore, being focused on faster growing Chinese and North American markets. One important driver here is the electric vehicle market – now a key target for players seeking to advance their position in premium tires. Unlike dominant China and fast-growing US, Europe’s EV industry is being hampered by a lack of strategic policy in the region.
10. Your suggestions
Tariffs and other trade barriers
Feedback from readers pointed to the increasing use of tariffs and other trade barriers as another particularly significant trend in 2023.
Among the countries/regions announcing tariffs during the year were: Brazil (natural rubber from various countries), China (halobutyl rubber, chloroprene from various countries), India (NR, butyl rubber, halobutyl rubber, TPUs from various countries) South Africa (PCR, TBR tires from China).
There was also the EU’s reimposition of duties on imported TBR tires from China, in April, following a legal glitch in previously applied anti-dumping and related trade protection measures. The same month saw the US retain antidumping and countervailing duties on off-the-road tires from India following a five-year (sunset) review. However, perhaps the most significant development was the US launch of an investigation into imports of TBR tires from Thailand - an important production location for major Chinese tire makers - with a final determination expected by Q3 2024.
Keep an eye also on the EU’s Carbon Border Adjustment Mechanism (CBAM) which this year will start to put a price on the carbon emitted during the production of carbon-intensive imports to the EU. The gradual introduction of the CBAM is aligned with the phase-out of the allocation of free allowances under the EU Emissions Trading System (ETS) to support the decarbonisation of EU industry. The mechanism will initially apply to cement, iron and steel, aluminium, fertilisers, electricity and hydrogen but when fully phased in is expected to capture more than 50% of the emissions in ETS covered sectors.
Wishing all ERJ readers a happy and successful 2024.