Desma advances ‘flexible’ moulding machine for large gaskets
11 Oct 2024
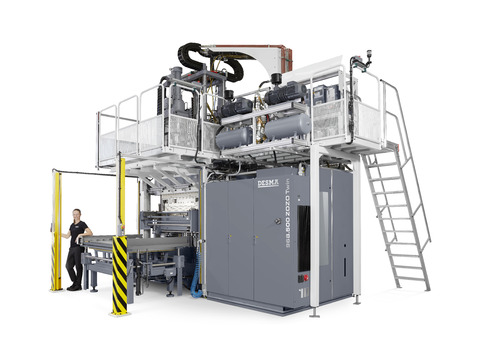
Responds to “dynamic” trends in the field of battery gaskets, which are reducing demand for machines tailored to specific products
Fridingen, Germany – Klöckner Desma Elastomertechnik GmbH (Desma) has claimed a significant advance with the introduction of a new machine designed specially for the production of large gaskets.
Labelled the Desma 968.500 ZOZO Twin (S3), the newly developed machine also offers “new flexibility for future requirements or a very universal applicability,” according to the German rubber moulding machinery maker’s 2 Oct announcement
Current “dynamic” developments in the field of battery gaskets in particular, “mean that there is less and less demand for specialised machines tailored to a specific product in order to minimise the risk of a product change,” Desma noted.
With a clamping force range from 5,000kN to 7,000kN, the unit extends the company’s established position in the supply of machines for the large seal sector and has already been delivered to an international customer.
The redesigned clamping unit – with two fixed, large-dimensioned, fully hydraulic clamping cylinders – is said to ensure “enormous deflection resistance” for optimum injection results.
The machine platform can be designed with one or two FIFO-B injection units, while both lift-off injection units can be moved to different positions on a sliding system, continued Desma.
With the design, it added, moulders can switch from decentralised double-injection to central-injection within a few minutes and conversion “from solid silicone with tamping device to rubber” can also be quickly carried out.
Another feature is an integrated mould-plate shifting device. This enables de-moulding or insert placement in the outer station via two mould base plates or mould centre plates, while the next injection cycle is already being completed inside the machine.
The heating plates inside the mould carrier and in the outer station are designed with six control zones in order to achieve “the best possible” temperature homogeneity, Desma also stated.
With the upgraded DRC 2023 TBM control unit, users can now decide whether the operator login and password level definition should be carried out via USB stick or, as a completely new feature, via RFID cards.
In addition, a function has been integrated that allows the user to configure RFID cards or similar directly on the machine OP, according to the manufacturer.
Meanwhile, the EnergyControl+ system developed by Desma is said to ensure “optimum energy consumption in every case, including all connected media, and provides a clear picture of the actual consumption.
This functionality is delivered through “real measurement with extensive built-in sensor technology and automatically optimizes all consumers installed in the machine.”