Elastomer ink to 'rewrite rules' for 3D-printed devices
10 May 2024
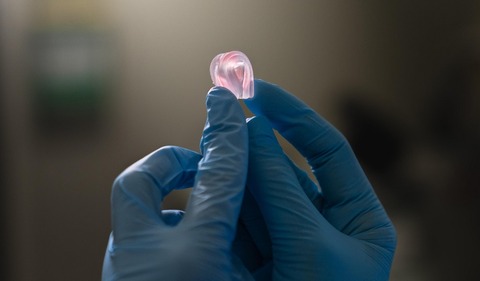
Swiss team says 'double network' materials can vary their mechanical properties to an "unprecedented" degree...
Lousanne, Switzerland: Researchers at the Swiss EPFL are targeting a new generation of soft actuators and robots with an innovative elastomer-based ink tailored for 3D printing of highly flexible objects.
Termed 3D-printable double network granular elastomers (DNGEs), the materials “can vary their mechanical properties to an unprecedented degree,” said Esther Amstad, head of the soft materials lab in EPFL’s school of engineering.
In one example, DNGEs were used to print a prototype ‘finger’, complete with rigid ‘bones’ surrounded by flexible ‘flesh’, according to release from Lousanne-based EPFL.
The ‘finger’, it said, was printed to deform in a pre-defined way, demonstrating the technology’s potential to manufacture devices that are sufficiently supple to bend and stretch, while remaining firm enough to manipulate objects.
The key to the DNGEs’ versatility lies in engineering two elastomeric networks.
First, elastomer microparticles are produced from oil-in-water emulsion drops and placed in a precursor solution, where they absorb elastomer compounds and swell up.
The swollen microparticles are then used to make a 3D printable ink, which is loaded into a bioprinter to create a desired structure. The precursor is polymerised within the 3D-printed structure, creating a second elastomeric network that rigidifies the entire object.
While the composition of the first network determines the structure’s stiffness, the second determines its fracture toughness.
The two networks can, therefore, be fine-tuned independently to achieve a combination of stiffness, toughness, and fatigue resistance.
With these advantages, the researchers believe that DNGEs could facilitate the design of soft actuators, sensors, and wearables free of heavy, bulky mechanical joints.
The lab is now working on the next steps toward developing such applications by integrating active elements – such as responsive materials and electrical connections – into DNGE structures.
Image: DNGE prototype ‘finger’ with rigid ‘bones’ surrounded by flexible ‘flesh’ © Titouan Veuillet