Ability to manage and offset higher materials, energy, labour costs will be key to maintaining profitability this year
In general, the business trend among the world’s largest tire manufacturers was upwards in 2022, with double-digit increases in sales for nearly all major players compared to the previous year.
When it came to earnings, however, there were major exceptions to the positive trend: Goodyear Tire & Rubber Co. and Sumitomo Rubber Industries in particular posting substantial declines.
Based on commentaries in the results statements from tire manufacturers, the key to maintaining profitability in 2022 was the ability to pass on sharp cost rises to customers – as well as progress in increasing the proportion of high-value tires in the sales-mix.
The impact of rising materials prices can be clearly seen at Michelin, which estimated the cost of raw materials ‘reported in cost of sales’ at €6.7 billion in 2022 versus €5.0 billion in 2021.
That is after factoring in all materials purchases, production and sales volumes, the valuation of raw materials, semi-finished and finished and product inventories. This included a €1,194-million hike in raw materials prices compared to 2021.
Further impacts
In 2023, Michelin anticipates a further negative impact from inflation in raw materials, transportation, energy and labour cost on its results. However, it expects to offset these increased costs by “enhancing its product mix and disciplined implementation of its pricing policy.”
At Bridgestone, ‘conversion costs’ increased by Yen69 billion in 2022, the group reporting: “Energy costs at plants rose sharply amid high crude and natural gas prices in 2022.” The trend, it added, is expected to continue this year.
In 2023, Goodyear said it expects its raw material costs to increase by around $200 million compared to 2022 – including the impact of a stronger US dollar and higher transportation and supplier costs.
The US tire maker reported “$890 million of year-over-year incremental costs during 2022 related to inflation and other cost pressures, primarily higher transportation and energy costs.”
Much of these costs stemmed from Europe, where chairman and CEO Richard Kramer noted “big energy inflation in the fourth quarter driven by the [Ukraine] war.”
Moreover, the Goodyear leader reported reduced consumer demand due to rising energy bills, leading to “really weak markets in the consumer replacement business, particularly in November and December.”
Headwinds continue
With these headwinds set to continue into 2023, Kramer said Goodyear is taking “appropriate actions to make sure we don’t build excess inventory, focus on cash and continue to look at more cost areas.”
Pointing to a 1 Jan list price increase of 5% in the European consumer replacement market from 1 Jan, Goodyear CFO Christiana Zamarro expected: “Europe to begin to catch up with the increases in raw-materials over the course of the first-quarter and second-quarter.”
Zamarro went on to forecast a “very significant step-down in raw-material price increases between the first and second quarters of 2023, that should be a benefit for us as well.”
At Continental’s Tire business, meanwhile, business performance was significantly impacted by price rises for important raw materials as well as higher energy and logistics costs.
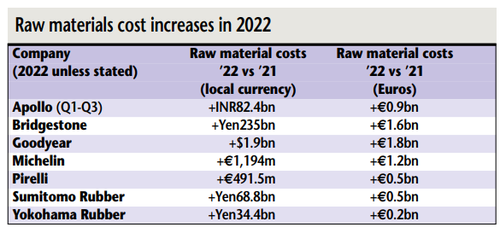
Prices for butadiene and ‘input products’ based on crude oil were particularly affected, the group noting a €2.3-billion cost headwind for its Tires and ContiTech business units combined.
In the tires business, however, Continental said that earnings were propped up worldwide by price adjustments as well as higher sales volumes of larger and high-margin tires in 2022.
Italian group Pirelli reported an increase of €491.5 million in raw materials costs in 2022 and production costs €327.4 million higher compared to the previous year.
For 2023, Pirelli expects a headwind ‘in terms of inflation’ of around €350 million, according to Andrea Casaluci, general manager operations at the Italian group.
The increase will stem mainly from: raw material costs, which are projected to account for 37% of group sales: energy cost inflation of around €100 million; logistics around €40million; and labour costs, €95 million.
These headwinds, though, are expected to be more than compensated for by efficiency plans and price/mix improvements, Casaluci pointed out.
Sumitomo Rubber Industries linked its sharp decline in profitability to inflationary trends and interest rate hikes, as well as the impact of the war in Ukraine.
Furthermore, the Japanese group noted “adverse trends around foreign exchange and prices and soaring costs for freight, raw materials and energy.”
Rising input costs were, of course, not the only factor impacting business performance among tire makers in 2022 – as evidenced, for example by Finnish group Nokian, which linked a 32% decline in earnings largely as well to its withdrawal from Russia – a factor likely to also impact other tire makers’ results in 2023.
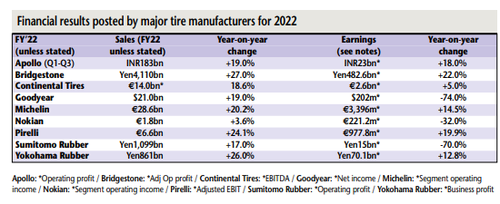