Sustainability in synthetic rubber plants through advanced process technology
12 Dec 2022
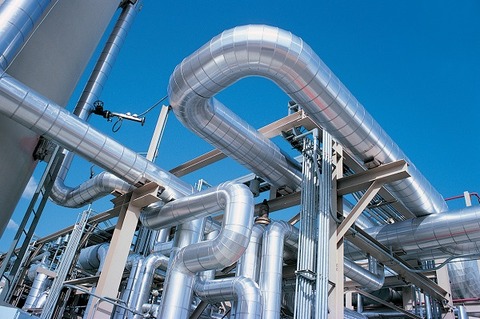
With updated processes, traditional plants can achieve major improvements in terms of energy consumption, efficiency and productivity, writes Dr. Walter Ramirez
Companies and countries have announced ambitous goals to increase circularity, beyond their net-zero targets, and to become climate-neutral by 2050. In line with this target, the conservative elastomers and rubber industry must invest in technologies to support this goal.
Some of the process technologies still in place date back to the 1960s. The time has come to take processes and operations to the next level, through implementing best-practices for process improvement and innovative designs for sustainability.
Sustainability is driven by legislation, the positioning of customers in the value-chain and, increasingly, by pressure from end-market consumers. The industry will face a gradual increase in more rigid emissions-reductions requirements as more customers pursue net-zero strategies and demand zero-carbon materials-services.
This is good news because it will enable an acceleration in the adoption of existing and new process technologies to make our industry greener by optimising for maximum flexibility and performance, while minimising energy-consumption, emissions, waste, and costs.
This should also drive the implementation of emissions-reduction initiatives – such as via direct devolatilisation and thermal energy electrification – as well as the adoption of sustainability practices, including mass-balance, renewable raw materials-energies, and zero-residues.
There is, therefore, a clear opportunity for operators to revamp current processes towards providing more flexibility, differentiation, and cost-effectiveness, complying with today’s goals and regulatory challenges.
Moreover, these capex projects will not only reduce the impact of synthetic rubber production on the environment but also minimise community impacts, secure social licenses to operate, and reduce costs.
Solution polymerisation
The solution polymerisation process – anionic, cationic, coordination to obtain SSBR, BR, SBS, SEBS, SEPS, SIS – offers unique possibilities and presents significant areas of improvement from the process perspective:
> Operation flexibility: Swing for batch, with the possibility to switch from rubber (i.e. SSBR) to elastomers (i.e. SBCs) in the same line.
> Solvent selection: The best solvent type must be properly selected depending on weather conditions, for low-energy solvent removal conditions, and also to enable crumb morphology control during the downstream process.
> Purification: The final product performance and quality, the polymer structure, and the process consistency depend directly on the purity of the raw materials. High monomer and solvent purity ensure high-purity blocks, structure control, and enhanced performance (differentiating against “commodity” type products). Improvements to column design and the number of stages can be implemented for maximum solvent recovery and highest purity, with low energy consumption. The designs must eliminate water traces (<1ppm moisture max.) and prevent column oversaturation, by implementing molecular sieves with an efficient regeneration system. These measures will lead additionally to the complete elimination of heavy species, to achieve greater consistency, lower emissions, and reduced cost.
> Reaction: A more efficient reactor design with an optimum agitation system with the right hydrodynamics for self-cleaning, to manage efficiently even at high solids content, with optimum heat transfer for maximum heat dissipation. The advanced reactor design must enable superior kinetic and polymer-structure control, employing (a) a catalyst or initiator titration system to ensure very precise additions; (b) a smart addition system for polar modifiers that will facilitate shorter cycles and increased productivity; (c) a control loop analysis system to follow the kinetics.
> Stripping: An optimised design and array to generate crumbs with low thermal history (to prevent colour and gel formation), has an optimised number of stages, with adjusted residence time, temperature, and additives for energy efficiency, enhanced water recovery, and fines reduction. An improved stripper geometry and agitation system, using eco-friendly additives, eases degassing, maximizes solvent recovery, and enables crumb morphology control.
> Finishing: Optimised crumb feeding systems for maximum productivity, with special screw and cutter designs, control the density of bales, to obtain friable bales. High-density, porous (fluffy) crumbs can be controlled with the proper equipment and conditions. New shafts have been designed for expellers and expanders. The advantages of these shafts: (a) provide a net increase in process productivity (>10%); (b) avoid gel formation; (c) eliminate surging; (d) reduce fines; (e) reduce hopper back pressure; (f) stabilise the finishing line; (g) increase longevity.
> Direct devolatilisation: This type of process technology is focused on thermoplastic rubber and enables the elimination of the stripping and finishing stages to obtain the final product. Direct devolatilisation represents the next generation of finishing because of the advantages of energy, throughput, environmentally friendly, quality, consistency, and compact pellet. Energy savings (60%) vs. the steam stripping processes have been confirmed. Steam consumption reduction (60-80%), water consumption savings (99%), and overall energy savings (60%). The production of dense or porous pellets is possible through special devices. These technologies have increased in performance and are now capable of handling low and very high viscosities, stably, at high throughputs, and a reasonable cost. Limitations include polymer characteristics (especially with polymers of high molecular weight and low melt flow index), the removal of salts and additives, and the “porous crumb” feature.
Emulsion polymerisation
The emulsion polymerisation process – cold, hot, to obtain ESBR, NBR, HNBR, SB latex – has not evolved substantially, except for optimised compositions. Areas for significant improvements to the process include:
> Reactor: The new emulsion polymerisation reactor is designed to efficiently control kinetics at the highest solid content and minimize coagulum, and scaling, combining cryogenic and high-temperature features. The implementation of pre-emulsion, degassing systems, and online loops to control kinetics, particle size, and distribution, are possible. Flexible chain design allows batch-continuous operation, and efficient product switching. Implementing higher solids formulations is possible by using an optimum hydrodynamic system, feeding policies, and additives.
> Stripping. The first stripping process was patented in 1942 for emulsion polymers and is basically how most plants operate today. An optimised finishing and stripping to remove residual monomer with low thermal history have been proposed, with an optimised monomer purification for recycling with maximum quality. New, proven industrial designs for butadiene recovery using an advanced compression-condensation system and a flash-flash-decanter system for Styrene recovery have been successfully implemented. Novel designs to maximise monomer removal by combining the stripper with spray nozzles connected to a distillation column (in the same equipment) have been proposed. Technologies for continuous coagulation-washing-dewatering-drying (i.e. self-cleaning, intermeshing kneaders with twin-screws, biaxial extruder barrel,) have been implemented.
> Concentration. The new emulsion polymerisation design can handle latex formulations up to 60-63% solids. This can be achieved by optimising the design, formulation, and conditions of the thin-film evaporator.
Fundamental transformation
The drive to enhanced sustainability will require a fundamental transformation of the elastomer and rubber industry: assessing and reducing environmental impact offers both great opportunities and great challenges.
Companies must, therefore, take action to decarbonise profitably, by exploring technological options for new processes to achieve sustainability goals, embracing a bold new vision of the future based on sustainable- and safe-design process technologies.
Implementation of best process and operational practices for more flexible, modular cost-effective synthetic rubber production with reduced environmental impact requires a mindset change to build a “green business.”
About the author
Dr. Walter Ramirez is co-founder and chief innovation officer of Innventik SL, a consulting and engineering firm that assists customers worldwide, to accelerate commercialisation & innovation projects. With bases in Spain and Mexico, Innventik services ranges from process assessment, FEED and EPC to business development and technology-market Intelligence in áreas including elastomers, polymers, nanotech, adhesives and tires. The firm’s recent/current projects in the synthetic rubber industry include a 100 kilotonnes per annum (ktpa) Nd butadiene rubber plant – start-up this year – and a 60ktpa SSBR & SSBR-F plant scheduled for start-up in 2023.