Elastomers for Sustainability (E4S) IV
28 Jan 2022
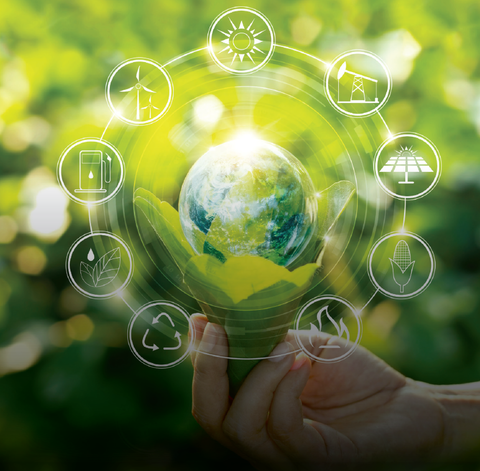
The 10 most important sustainability projects happening in the elastomers/rubber industry right now
London - The Top 10 ranking of projects for the fourth staging of the Elastomers for Sustainability programme have been published in the Nov/Dec issue of European Rubber Journal magazine.
E4S is an industry-first sustainability initiative, designed to highlight significant advances for elastomer end-user sectors including automotive, tires, construction, consumer, industrial and medical.
E4S IV table
JSR Elastomer Europe - New hydrogenated styrene-butadiene rubber
While wear resistance of tires can be improved by increasing molecular weight, this reduces rolling resistance due to the lower number of functional groups at the polymer chain-ends. High levels of filler can also improve wear properties, but rolling resistance is again deteriorated.
To solve this trade-off relationship, JSR developed a newly hydrogenated polymer with a unique polymerisation technology, which controls the number of crosslinking points. The resulting uniform crosslinked structure allows ‘stress minimisation’ to help improve wear resistance by 50%.
Moreover, explains JSR, the single bond after hydrogenation allows free rotation leading to high polymer entanglement, which can contribute to high modulus and better wear resistance.
JSR said its hydrogenated SBR has been successfully commercialised, and expected applications in a range of tire-types.
The technology can, therefore, contribute substantially to sustainability, by increasing fuel efficiency, lowering materials-use, reducing microplastics and extending lifecycle up to 1.5 times that of conventional tires.
As for the rolling resistance, the new polymerisation technology is said to deliver a 30% improvement compared to conventional SBR.
Key to the improved properties, so, are: entanglement density; cross-linked structure: and the number of unsaturated bonds
At JSR, entanglement density was estimated by dynamic viscoelasticity measurements with non-cured samples. Tests showed this to be much higher than with conventional SSBR.
The uniform cross-linked structure was estimated via AFM nanoscale imaging, which showed more uniform moduli in the hydrogenated polymer. Meanwhile, the effect of the number of unsaturated bonds was confirmed by tests showing improved ozone resistance for the HSBR.
JSR also analysed the effect of unsaturated bonds by S-S curve before and after tire driving tests with HSSBR and conventional SSBR. This showed that a tire with HSSBR can reduce chemical changes in the compound during driving and, so, extend tire-life.
Nynas - New bio-based processing oil
For E4S III, Nynas entered a bio-based alternative (branded Nytex BIO 6200) to commercially available tire oils, which are mostly based exclusively on crude mineral oil technology.
According to Nynas, its bio-based plasticiser for the tire & rubber industries features a substantial amount of bio-based content while matching the performance of the best performing conventional tire oils.
The product can also completely replace currently used products, such as TDAE, RAE etc without compromising productivity and without changing production processes.
The product is available globally on a commercial scale, and is being offered to tire makers, producers of rubber goods, producers of synthetic rubber (as an SBR-extender) and adjacent industries (eg as a carrier for insoluble sulphur).
Nynas has now supplied data on uses in a high performance summer tire tread compound and in a European winter tire tread compound where it was shown to outperform conventional tire oils.
Nynas also reported successful results for the oil in studies of tire compounds containing other sustainable raw materials, such as Guayule rubber and rice husk silica. Case studies were also provided for non-tire applications, such as anti-vibration mounts.
The company also pointed to its investments in recent years, including an upgrade of its Gothenburg refinery with energy-efficient furnaces to cut CO2 emissions, as well as personnel resources in the area of sustainable development.
UPM Biochemicals GmbH - Renewable functional fillers
The project features the conversion of sustainably sourced wood via new biorefinery processes and technologies. The end-product is a “revolutionary”, wood-based renewable functional filler (RFF) suitable for a broad range of elastomer applications.
UPM says RFFs can partially or fully replace traditional functional fillers, including carbon black and silica, in applications, including tire, automotive, flooring or footwear.
RFFs are said to deliver performance benefits including: weight reductions via significantly lower material density; enhanced electrical insulating properties; and absence of polycyclic aromatic hydrocarbons (PAH)s. Material density is ≤ 1.35 g/cm³ and hence at least 25% lighter when compared to conventional fillers used by the rubber industry.
In its E4S project updates, UPM said it is working with OE’s and tier 1s & 2s to approve the product and is “at a much advanced stage” with these programmes.
In October 2020, UPM held a ground-breaking ceremony for a E550-million wood-based biorefinery at Leuna, Germany. RFFs will represent a “significant proportion” of output from the 200ktpa facility, slated for start-up in late 2022.
RFFs are currently produced at a pilot-scale of several tonnes, which allows material testing as well as product and application development activities.
UPM also invested in a larger pilot plant in Finland, due to be operational by Q3 2021 and established a rubber technical centre in Leuna, equipped with modern compounding and testing equipment.
In its latest update, UPM reported that it is in contact with over 40 global leading rubber parts manufacturers, with more that 10 potential players already performing industrial-scale trials using RFF.
ETB - Bio-butadiene from ethanol for tire production
An early pace-setter in the E4S programme, ETB’s project targets the construction of standalone bioethanol-to-butadiene plants and those integrated into fossil-based butadiene production sites.
To deliver this, the Russia-based team developed a new catalyst system to increase the energy-efficiency and bio-butadiene yield of the Lebedev process.
The results offered significant enhancements to sustainability indices across the synthetic rubber production chain – with clear benefits also for the ethanol industry.
At the time of the original project entry, commercialisation steps included an engineering project for a demo plant in The Netherlands, with first commercial-scale batches expected within two to three years.
The Russian company has since announced a collaboration with Trinseo to explore commercialisation of the technology. This envisages the start-up of a pilot plant, employing technology from both companies, to produce the bio-BD from ethanol feedstock via ETB’s catalyst and single-stage process technology
Quite recently, ETB has also signed commercial agreements towards establishing a facility at a major European petrochemicals site, and also reported strong demand for its bio-based monomers from the synthetic rubber industry.
Asahi Kasei - New SBC for polymer modified bitumen
Asahi Kasei has weighed in with a new application for its styrenic block copolymer technology, employing advanced partial-hydrogenation and functionalisation chemistries.
The molecular architecture is said to reduce the mixing temperature with bitumen and the amount of polymer added. It also lowers degradation via aging and enhances adhesion to aggregates, thereby extending service-life of pavements.
In recent years, notes Asahi, there have been growing demands for polymer modified bitumen (PMB) to reduce mixing temperature, save materials, and improve physical properties and durability of pavements.
To meet these demands, Asahi’s R&D team focused on reducing unsaturated double bonds, which are vulnerable to degradation, and developed a functional group to enhance adhesion to aggregates.
While aging resistance was improved by fully hydrogenating the SBS, lowering the polarity led to crystallisation so that the compatibility with bitumen was significantly reduced.
To overcome these problems, Asahi developed a special hydrogenation catalyst and a novel production technology to control the partial hydrogenation rate. These have made it possible to retain double bonds without excessive reduction in compatability.
In addition, the company developed a special functional group that achieves a strong polymer-aggregate interaction to improve rutting and cracking resistance.
The resulting polymer is said to contribute to energy saving, material saving, high durability in the aging of PMBs, and increased dynamic stability of mixtures.
According to the company, the newly launched SBC is “now being used and tested by many customers worldwide and has received positive feedback.”
The next goal, it stated, is “to improve the performance of recycled or poorly performing bitumen, and to increase the percentage of sustainable raw materials (monomers).
Techsyn - New tire technology platform for improved sustainability performance
Techsyn is a tire technology platform combining optimised synthetic rubbers from Arlanxeo with tailor-made silica from Solvay and improved mixing technology from Bridgestone. Launched 23 Feb, the technology can increase wear-efficiency by up to 30% and decrease rolling-resistance by up to 6% compared to other Bridgestone EMIA summer tires – without any trade-off in other tire characteristics.
Impressively, the development project, involving cross-functional teams in different global locations, was conducted within 24 months.
This included development, testing, up-scaling and industrialisation of the new functionalised solution SBR rubber and modified silica product – and validation on Bridgestone’s side to develop the compound, and to design, upscale and commercialise the technology.
Bridgestone is to implement mass-production of Techsyn for various tire categories and vehicles: adapting the balance of rolling resistance, wear and wet grip to meet varying needs.
Versalis SpA - Styrenic block copolymers with improved sustainability
This development project aims to increase the sustainability of styrenic block copolymers (SBCs), using feedstock monomers obtained from renewable sources through the mass-balance approach.
The first technical challenge, said the company, was to manage a bionaphtha feedstock in Versalis’ cracking units to obtain – using additional standard petrochemical activities – intermediates and monomers for polymerisation.
The team applied a mass-balance approach, certified according to ISCC+ methodology, to obtain styrene and butadiene monomers to manufacture polymers via anionic polymerisation.
Products can be certified as “bio-attributed – BA” if the feedstock is based on raw materials from vegetable origin, or as “bio-circular attributed – BCA” if the feedstock is based on raw materials obtained from vegetable wastes.
Versalis said it can manufacture bio-naphta/ISCC+ grades of SBCs – and also random styrene butadiene polymers – using conventional facilities. The resulting “bio-attributed” materials are said to show the same composition and performance of fossil-derived polymers.
ExxonMobil - New specialty elastomer to enhance barrier of tire innerliners
This new elastomer has been developed to enhance the barrier performance of tire innerliners and, in turn, extend the battery range of electric vehicles.
An alternative to traditional halobutyl/natural rubber blends, Exxpro 3563 is a fully saturated elastomer produced by the carbocationic polymerisation of isobutylene and para-methyl styrene followed by halogenation.
The fully saturated backbone enables “exceptional” chemical and oxidation stability, while increased chain stiffness and better packing-density with benzylic bromide groups presents a highly effective barrier to oxygen molecules.
Compared to conventional innerliners, the new elastomer delivers: 20-50% improved air retention; a 12% improvement in in-use rolling resistance; on-target inflation pressure loss rate (IPLR) of <1.8% for global EV OEM leaders; and an increase of 3-7% in EV battery range.
Asahi Kasei - New-generation styrene-butadiene rubber
For the first E4S programme in mid-2020, Asahi entered its sixth generation functionalised SBR, which was stated to deliver 20% lower rolling resistance than the previous grade and reduced wear. For this, Asahi developed a special functional group to enhance filler-polymer interaction – to improve wear resistance and rolling resistance – and a new polymerisation technology to optimise the polymer structure for advanced abrasion resistance while maintaining processability.
Asahi has since reported that it is now introducing its 6th generation SBR to tire manufacturers around the world. The overall response, it said, “was very positive, and some grades will be commercialised in 2021/22.”
Tyromer - Tire-to-tire recycling
Tyromer’s devulcanisation technology uses twin-screw extrusion to carefully process ELT rubber crumb and other waste rubber – with encouraging results.
Since 2016, a facility within AirBoss Rubber has supplied tire-derived product (TDP) to KAL Tire, which has used it in an OTR retread compound with 20% content.
OTR, truck and passenger tires with 15-20% TDP are currently on road trials in North America and Europe and a passenger car tire maker is optimising a tire compound with 30% TDP.
A second TDP facility is starting up in Windsor, Ontario, Canada to supply a top American brand. With financial support from the Dutch government, a third TDP plant has been built in The Netherlands to supply a top brand in the EU.
In an update for E4S IV, Tyromer reported making “ a ton of progress [this year] as travel has opened up and we were able to get our facilities off the ground.”
E4S JUDGING
The expert panel, which was coordinated by ERJ editor Patrick Raleigh, comprised:
PROF JAMES BUSFIELD, professor of materials & national teaching fellow director of industrial engagement & head of the soft matter group, Queen Mary University of London.
CHRISTOPH SOKOLOWSKI, lead on ‘sustainability’ issues within the German rubber industry association the WDK (Wirtschaftsverband der deutschen Kautschukindustrie), based in Frankfurt am Main, Germany.
MARTYN BENNETT, who has recently founded UK-based consultancy Midsomer Science, after a career spanning over 30 years at Avon Rubber plc, most recently as chief scientist and head of its ARTIS consultancy service.
JIRÍ BREJCHA, head of Brejcha Rubber Consulting, and former materials development specialist at Trelleborg Wheel Systems, and before that Mitas, Prague, Czech Republic.