DKT: New LWB concept to raise efficiency levels
17 Jun 2022
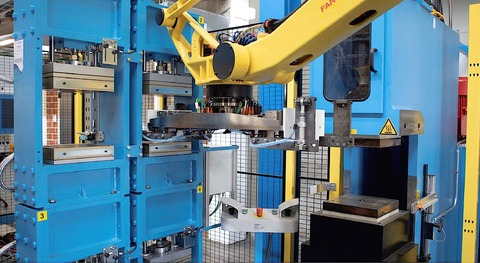
Approach involves separating the injection moulding cycle into individual processes
Nuremberg, Germany – Highlights on the LWB-Steinl stand at DKT include a novel concept for increasing the economic and technical efficiency of rubber injection moulding.
The approach involves separating the injection moulding cycle into individual processes with the option of subsequent re-combination to form a new sequence tailored to specific requirements.
LWB’s multi-station injection moulding system allows customers to start with “reasonably sized” moulds on a small machine and to ramp-up production by adding additional mould sets and external heating stations.
Machines are, therefore, used for injection only, freeing-up capacity for additional cycles – allowing greater flexibility, lower initial investment and the potential to increase production with incremental investment steps.
These advantages also work in reverse, if call-off volumes fall, with moulding capacity freed up for the production of similar parts, even if these have to be produced within a different cycle time.