EV batteries spark rubber innovation
1 Feb 2022
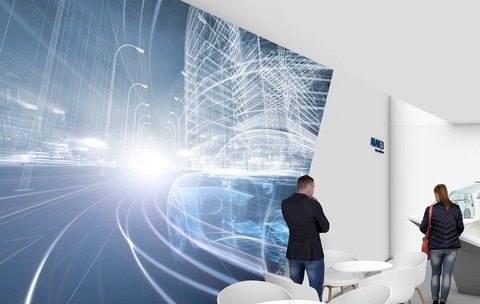
New mobility is driving innovative developments among suppliers and processors of rubber materials, equipment and end-use components
The ongoing shift away from petrol-driven engines is continuing to drive interesting technology developments across the automotive-rubber value-chain.
On the materials side, Arlanxeo says the electrification of vehicles requires a wide range of new product solutions adding that it “is actively working on these [developments] with partners around the globe.”
Over recent years, the synthetic rubber supplier has set up battery laboratories in Germany and China with specific focus on new product development, battery assembly and battery testing.
Arlanxeo is also active in several publicly funded projects, exploring opportunities to position high-performance elastomers in next-generation batteries, such as solid-state, lithium-sulphide or lithium-air batteries.
R&D teams, it said, are focused on areas such as the optimisation of elastomer compounds for use as binders for active materials or as dispersants for conductive materials in lithium-ion batteries.
Moreover, as batteries can represent a quarter or more of the total vehicle weight, light-weighting solutions are required, noted the company, which also pointed to its work in the reduction of vehicle noise and vibration.
“Batteries need to be mounted to the chassis and vibrations need to be controlled,” stated Arlanxeo. “The noise caused by the internal combustion engine is absent, therefore, sound from road contact and wind becomes more obvious and needs to be minimised.”
Equipment suppliers are also to the fore in the EV technology race, as evidenced by recent developments in the rubber moulding machinery sector.
Austrian company Maplan has designed a massive new injection moulding machine for the production of battery seals specifically for the automotive industry. The 100-tonne model is the biggest ever machine to leave its production hall in Austria (see panel).
And, German rubber moulding machine specialist Desma has recently highlighted the role of its technology in the production of seals for automotive fuel cells.
“Wafer-thin” liquid silicone rubber (LSR) seals are applied to the hundreds of bipolar plates used in the engine of fuel-powered passenger cars.
Typically on the Desma machines, a two-component LSR is injected with high precision on both sides and vulcanised, explained a recent technology note on the Desma website.
“The size of the machines varies, depending on the size and number of inserts. This process can be fully automated with the aid of robotic systems,” Desma pointed out,
Silicone is also focus for Swiss processor Datwyler, which is set to start production of LSR components in Wuxi, China in early 2022 – to support customers in the world’s most dynamic new-mobility market.
The ability of LSR to perform in temperatures ranging from -55 ?C to +250 ?C and high-level electrical insulation properties will be key to many evolving EV applications, such as HV-connectors, e-motors and driver assistance systems, it noted.
More generally, Altdorf, Switzerland-based Datwyler is expanding its materials capabilities in order to meet the challenges posed by the shift to new mobility – with a particular focus on battery sealing technology.
With project ETEMI – electrically and thermally conductive and electromagnetic interference (EMI) shielding materials – the company is exploring “entirely new categories” of elastomers, liquid silicone rubber and thermoplastic compounds.
In particular, the project aims to provide “system critical sealing components with enhanced functionality” to customers diversifying towards hybrid and battery electric vehicles.
“As the trend towards electrification continues to gather momentum, the ability to conduct electricity and heat, as well as to shield certain components from electromagnetic signals, is increasingly important,” the company said
The ETEMI project, it added, ultimately aims to create a material matrix whereby electrical and thermal conductivity and EMI shielding can be coupled and decoupled to suit a wide variety of applications.
Thermal management of an electric vehicle battery, it explained, could be managed in part by the sealing material, while EMI shielding could be introduced via sealing technology for sensitive components, such as sensors and control devices.
Electrical conductivity for discharging and antistatic materials is another target. Here, Datwyler said, its technology can enable the removal of certain components, such as metal conductors, thus delivering weight-reductions.
Already, said Datwyler, the ETEMI project has advanced its capabilities in areas, including the in-house mixing of specialist compounds and the design of mixing programmes as well as analysis & testing of new materials for the stringent regulations required by e-mobility.
An entirely new approach to powering EVs is among the areas being explored by Hutchinson SA, which has partnered with the Israeli start-up Electreon to advance an innovative wireless battery charging system.
The Electreon Wireless technology features a ‘shared energy platform’ which charges vehicles ‘on the go’ through a complete wireless electric-road system.
The system involves under-road units of copper coils which transfer energy from the electricity grid to the roads and approaching vehicles.
French rubber-components major Hutchinson is supplying ‘rubber-encapsulated’ inductive segments, which transfer the energy to the vehicle’s receiver.
If successful, the technology could help automotive manufacturers reduce the size and weight of onboard batteries, while also freeing up space for vehicle fittings.
In a statement, Hutchinson said it is supporting Electreon’s development internationally with the help of its centre for research and innovation as well as its locations globally.
“This partnership allows the two companies’ technological, industrial and geographical strengths to be combined to contribute to the development of sustainable mobility,” the company added.
Electreon’s technology was first installed in Tel Aviv and has now been employed in Karlsruhe, Germany; Lombardy, Italy and in Sweden, according to Hutchinson.
In the US, meanwhile, researchers at the Georgia Institute of Technology have developed rubber electrolytes for EV batteries, which they say will make them more cost-efficient, safer and longer-lasting.
The project is part of an ongoing collaboration with SK Innovation, part of Seoul-based chemicals giant SK Group, which is focused on the commercialisation of new solid-state battery technologies.
The research, conducted in collaboration with the Korea Advance Institute of Science and Technology, replaced liquid electrolytes with unspecified “rubber-based polymers”. These were found to act as “superhighways” for fast lithium-ion transport “ with superior mechanical toughness resulting in longer charging batteries.
In conventional lithium-ion batteries, ions are moved by a liquid electrolyte. However, as the battery is inherently unstable, the slightest damage can leak into the electrolyte, leading to explosion or fire.
Due to such safety issues, the automotive industry is now looking into solid-state batteries, which can be made using inorganic ceramic material or organic polymers.
Currently, the main focus is on building inorganic solid-state electrolytes, said Seung Woo Lee, associate professor at the George W. Woodruff School of Mechanical Engineering.
But, he added, these materials are “hard to make, expensive and are not environmentally friendly.”
According to the research team, rubber-based organic polymers are potentially superior to other materials due to their low manufacturing cost, non-toxicity and soft nature.
However, conventional polymer electrolytes do not have sufficient ionic conductivity and mechanical stability for reliable operation of solid-state batteries.
To address that issue, the team allowed the material to form a 3D interconnected plastic crystal phase within the robust rubber matrix.
“This unique structure resulted in high ionic conductivity, superior mechanical properties and electrochemical stability,” said the Georgia Tech statement.
The rubber electrolyte, it noted, can be made using a simple polymerisation process at low temperature conditions, generating “robust and smooth interfaces” on the surface of electrodes.
The rubber electrolytes prevent lithium dendrite growth and allow for faster moving ions, enabling reliable operation of solid-state batteries even at room temperature.
“Rubber has been used everywhere because of its high mechanical properties, and it will allow us to make cheap, more reliable and safer batteries,” said Lee.
“Higher ionic conductivity means you can move more ions at the same time,” said Michael Lee, a mechanical engineering graduate researcher.
“By increasing specific energy and energy density of these batteries, you can increase the mileage of the EV.”
Project backer SK Innovation is building a new EV battery plant in Georgia, US to produce an annual volume of lithium-ion batteries equal to 21.5 Gigawatt-hours by 2023.
“All-solid-state batteries can dramatically increase the mileage and safety of electric vehicles,” said Kyounghwan Choi, director of SK Innovation’s battery research centre.
“Fast-growing battery companies, including SK Innovation, believe that commercialising all-solid-state batteries will become a game changer in the electric vehicle market,” he added.